The Role of Polyurethane Adhesives in Automotive and Aerospace
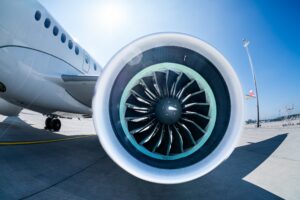
Lightweight materials, structural integrity, and long-lasting durability are fundamental in the automotive and aerospace industries. Polyurethane adhesives have gained prominence in the automotive and aerospace sectors due to their strength, flexibility, and durability. These properties are essential for bonding critical components that must withstand high levels of stress, extreme temperatures, and other challenging conditions.
Why Use Polyurethane Adhesives in Automotive and Aerospace?
Polyurethane adhesives offer distinct benefits for automotive and aerospace applications due to their superior mechanical properties and adaptability. They provide:
- High Bond Strength: Polyurethane adhesives form a strong bond that can support the weight and stress of various components.
- Flexibility and Vibration Resistance: These adhesives can absorb shocks and vibrations, a critical feature for vehicle parts that are frequently exposed to motion.
- Temperature and Environmental Resistance: Polyurethane adhesives maintain their performance across a wide range of temperatures and resist exposure to chemicals, moisture, and UV radiation, making them ideal for both automotive and aerospace environments.
Types of Polyurethane Adhesives Used
Polyurethane adhesives are available in both one-part and two-part formulations, each suited for different bonding needs within automotive and aerospace manufacturing.
- One-Part Polyurethane Adhesives: These adhesives cure by reacting with moisture in the air, making them easy to apply without a separate hardener. They’re particularly effective for bonding large panels and structural components that require durable, long-lasting bonds.
- Two-Part Polyurethane Adhesives: Consisting of a resin and a hardener, these adhesives offer faster curing times and more controlled curing, ideal for applications requiring precision bonding or faster assembly processes. Two-part adhesives are commonly used in scenarios where components need to be assembled quickly and with high strength.
Applications in Automotive Manufacturing
In the automotive industry, the demand for lightweight materials and high-strength bonding has made polyurethane adhesives a preferred solution for joining various materials, including metals, plastics, composites, and glass. They are increasingly used in EV manufacturing to bond battery modules, which require secure and durable bonds that can resist vibrations, thermal expansion, and temperature fluctuations. They offer a strong, flexible bond that protects battery components from movement and mechanical stress, enhancing overall vehicle performance and safety.
Key applications include:
1. Body and Frame Assembly
Polyurethane adhesives are used to bond panels, frames, and other structural components in vehicle bodies. They provide several advantages:
- Enhanced Durability: The adhesive forms a robust bond that can withstand the impacts and stresses experienced during vehicle operation.
- Reduced Weight: By bonding materials like aluminium and composites, polyurethane adhesives help reduce vehicle weight, improving fuel efficiency and performance.
- Improved Aesthetics: Polyurethane adhesives create smooth, clean joints that don’t require additional fasteners, contributing to a streamlined appearance and reducing the likelihood of corrosion.
2. Glass Bonding
Polyurethane adhesives are also widely used for bonding windshields, windows, and other glass components, providing:
- Weather Resistance: These adhesives prevent moisture infiltration and help maintain the structural integrity of glass components, even in extreme weather.
- Impact Resistance: Polyurethane adhesives absorb vibrations and resist shocks, protecting glass from cracking or loosening during vehicle operation.
- UV Stability: Since glass is often exposed to sunlight, the UV-resistant properties of polyurethane adhesives ensure they do not degrade, preserving the bond strength over time.
3. Interior and Trim Bonding
Polyurethane adhesives provide flexibility for bonding interior parts, including seats, dashboards, and trim elements, where flexibility and aesthetic quality are crucial.
- Noise and Vibration Dampening: Polyurethane’s flexible nature helps absorb sound and vibrations, making for a quieter, smoother ride.
- Long-Lasting Bonds: For interior components, polyurethane adhesives offer longevity without cracking or becoming brittle, even under prolonged exposure to temperature changes.
Applications in Aerospace Manufacturing
In aerospace, where component performance and safety are critical, polyurethane adhesives serve a key role in bonding lightweight materials like aluminium and composites to enhance fuel efficiency and reduce overall weight. Polyurethane adhesives have been successfully used to bond fuselage sections and wings, ensuring stability while minimising weight. The adhesives’ resistance to environmental stressors, including UV radiation, extreme temperatures, and pressure changes, makes them essential for ensuring safe and long-lasting bonds in aircraft structures.
Examples of how they’re commonly used:
1. Structural Bonding
Aerospace structures demand adhesives that can bond metals, composites, and plastics with exceptional strength. Polyurethane adhesives excel in this area due to:
- High Strength-to-Weight Ratio: These adhesives offer strong bonds without adding extra weight, a crucial factor in aerospace applications where every kilogram counts.
- Resistance to Environmental Extremes: Aircraft components encounter intense variations in temperature, pressure, and UV exposure. Polyurethane adhesives maintain their properties under these conditions, ensuring safety and stability.
- Vibration Resistance: Airborne components are subject to frequent vibrations and stresses. The flexibility of polyurethane adhesives enables them to absorb these forces, reducing fatigue on bonded parts.
2. Sealing and Encapsulation
Polyurethane adhesives are also used to seal and encapsulate various components, protecting them from the harsh environments found in aerospace applications:
- Protection from Moisture and Corrosion: Polyurethane adhesives resist moisture and chemical exposure, helping to prevent corrosion and prolonging the life of components.
- Temperature Stability: They remain stable under the fluctuating temperatures experienced during flight, protecting sensitive parts from thermal stress.
3. Composite Bonding
The increasing use of composites in aerospace requires adhesives that can bond these materials securely while preserving their lightweight properties:
- Strong Bonding with Composite Materials: Polyurethane adhesives bond effectively with composites, supporting weight reduction and strength without sacrificing performance.
- Compatibility with Advanced Materials: As aerospace materials evolve, polyurethane adhesives can be tailored to match new substrate requirements, making them adaptable for future advancements.
Advantages of Polyurethane Adhesives in Automotive and Aerospace
Polyurethane adhesives offer several key advantages that make them invaluable in these high-performance industries:
- Weight Reduction: By eliminating the need for metal fasteners, polyurethane adhesives help reduce overall weight, which is especially critical in aerospace applications.
- Enhanced Durability and Longevity: They provide lasting performance, withstanding vibrations, thermal cycling, and mechanical stress over time.
- Corrosion Resistance: Since they form sealed, continuous bonds, polyurethane adhesives protect against moisture infiltration and corrosion, an essential feature for both automotive and aerospace durability.
- Streamlined Manufacturing: Adhesives enable manufacturers to reduce production times and costs by simplifying the assembly process and eliminating the need for welding or riveting.
Future Trends in Polyurethane Adhesives for Automotive and Aerospace
Polyurethane adhesive technology continues to evolve, with innovations focusing on sustainability, performance, and compatibility with advanced materials:
- Eco-Friendly Formulations: As the automotive and aerospace industries move toward greener practices, polyurethane adhesive manufacturers are developing low-VOC and solvent-free options that reduce environmental impact.
- Higher Temperature Resistance: Research is focused on developing polyurethane adhesives that can withstand even higher temperatures, which is especially valuable for high-speed aircraft and high-performance electric vehicles.
- Smart Adhesives: Advanced polyurethane formulations that incorporate self-healing properties or sensors for monitoring bond integrity could become more common, further enhancing safety and longevity in these industries.
With ongoing innovations and a growing focus on sustainable practices, polyurethane adhesives will continue to play a vital role in the development of next-generation vehicles and aircraft, supporting lightweight design, enhanced safety, and improved performance.
For more information on how Witton can address your manufacturing needs and improve visibility in your supply chain, contact us today. We’re ready to discuss how our expertise and advanced solutions can meet your specific requirements.